Caractéristiques indispensables d’un logiciel CFAO efficace pour la construction navale
La construction navale se distingue des autres industries construisant de grandes structures par plusieurs aspects importants. Pourquoi ? Quelles sont les spécificités de ces secteurs ? Pour être efficace, quelles sont les capacités d’un bon logiciel de CAO/FAO pour la construction navale ?
Après avoir travaillé pendant plus de 40 ans avec les équipes d’ingénieurs qui ont besoin de solutions de CAO et de FAO, chez Alma, nous connaissons maintenant les capacités qui sont essentielles pour un projet de construction navale.
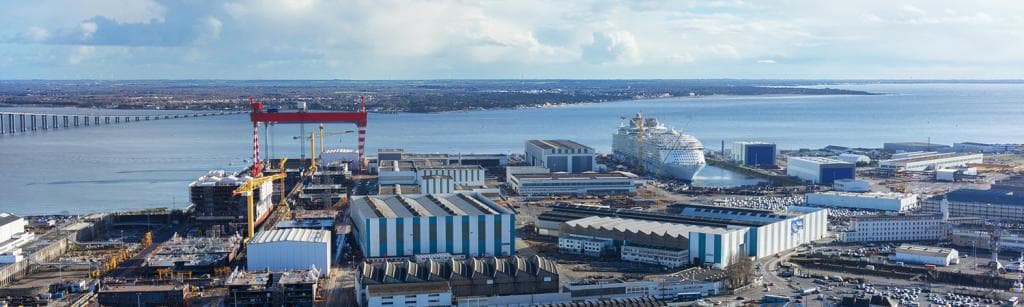
Qu’est-ce qui rend la construction navale différente ?
La construction navale se distingue par le fait que les navires et les structures offshore commencent souvent le processus d’ingénierie avant que la conception ne soit entièrement approuvée, et que la construction commence avant que l’ingénierie ne soit terminée. Il faut donc tenir compte des travaux d’ingénierie préexistants et des sections construites lors de la mise en œuvre des changements nécessaires.
En outre, la construction navale est régie par des réglementations spécifiques et des organismes de réglementation propres à l’industrie. Contrairement aux grandes installations terrestres, chaque navire est exploité dans des contextes environnementaux, réglementaires et politiques différents lorsqu’il voyage dans le monde entier, ce qui ajoute des niveaux de complexité que l’on ne retrouve pas dans d’autres projets de construction à grande échelle.
Dans ce contexte, les logiciels de CAO et de FAO sont essentiels à la réussite d’un chantier naval, car ils permettent de rationaliser la conception, d’améliorer la précision et d’optimiser les processus de production.
Un bon logiciel de CAO/FAO doit …
Tenir compte de la façon dont le navire est construit
Tout d’abord, il est important de comprendre comment les navires sont construits, car cela détermine les données (pièces à découper, stock de tôles et de chutes). Un navire est constitué de blocs, assemblés progressivement en commençant par le milieu, afin d’obtenir un bon équilibre. Chaque bloc est constitué de sous-ensembles, eux-mêmes constitués de planchers et de murs.
C’est pourquoi il est généralement recommandé d’organiser les données en blocs, afin d’éviter de mélanger des pièces de différents blocs dans les mêmes imbrications. Il est important de ne pas compliquer la logistique, qui est déjà très exigeante, et de simplifier le tri des pièces coupées afin qu’elles puissent être envoyées aux sous-ensembles où elles doivent être soudées.
De même, les besoins en matériaux, souvent calculés avant la fin de la conception détaillée du navire, sur la base des premières versions des pièces issues de la CAO, serviront à définir les stocks de tôles nécessaires à chaque bloc, sachant que des chutes récupérables peuvent parfois être transférées d’un bloc à l’autre.
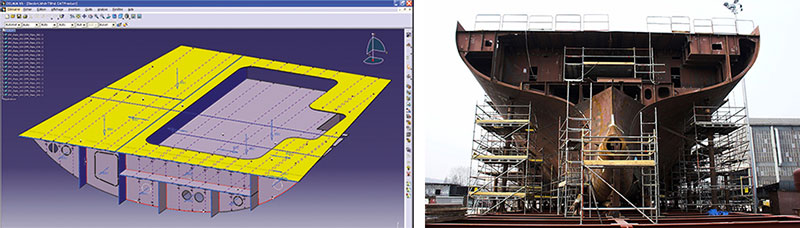
S'intégrer dans l'environnement informatique du chantier naval
Dans le secteur naval, la solution de FAO est l’élément final de la chaîne de fabrication et doit donc communiquer avec tous les systèmes de gestion de l’information utilisés par le chantier. Il s’agit d’importer les géométries des pièces à découper – dont nous parlerons juste après -, mais aussi d’importer la liste des pièces à produire, avec leurs informations de production (quantité, date limite, etc.), qui est souvent fournie par un système MRP ou PLM, indépendant de la CAO. De même, le stock de tôles est souvent géré par un MRP dédié avec lequel le logiciel de FAO doit s’interfacer pour importer les tôles emboîtables.
En retour, les résultats de l’imbrication (quelles pièces ont été découpées, à partir de quelles tôles, quelles chutes réutilisables ont été générées) doivent être exportés pour informer le MRP ou le PLM. Les programmes CN à découper doivent également être mis à disposition sur un poste de travail de l’atelier, accompagnés d’un document d’atelier souvent personnalisé, contenant toutes les informations utiles (identifiant de la tôle à découper, temps d’usinage, liste des pièces découpées…), afin que l’opérateur de la machine puisse lancer le programme de découpe.
Récupérer les données géométriques et d'usinage
Dès le premier projet de construction navale, nous avons commencé par définir un format neutre pour l’échange de données avec les outils de CAO afin de faciliter l’intégration. Puis, au fil du temps, nous avons développé des interfaces avec tous les systèmes du secteur, de sorte qu’aujourd’hui nous pouvons travailler avec n’importe quel chantier naval, quel que soit le système de CAO qu’il a choisi d’utiliser. Nous importons les géométries décrivant les pièces à découper, en les séparant si nécessaire dans le cas d’un DXF en plusieurs parties, et nous récupérons toutes les données d’usinage les plus couramment utilisées.
Ces données peuvent être les différents processus de marquage et de rectification, la grande variété de textes indiquant le nom des raidisseurs à souder, les axes du navire, les lignes de pliage, les propriétés de chanfrein appliquées à chaque bord, etc. Il faut cependant noter que lors du déploiement de notre solution, outre l’importation de la géométrie et de l’usinage caractérisant une pièce, il est presque toujours nécessaire d’adapter le processus d’importation et d’exportation des pièces à découper au processus opérationnel du chantier naval. Par exemple, comment gérer les modifications de pièces ? Est-il nécessaire d’invalider systématiquement les imbrications impactées par une pièce modifiée, ou est-il préférable de laisser l’utilisateur le faire ?
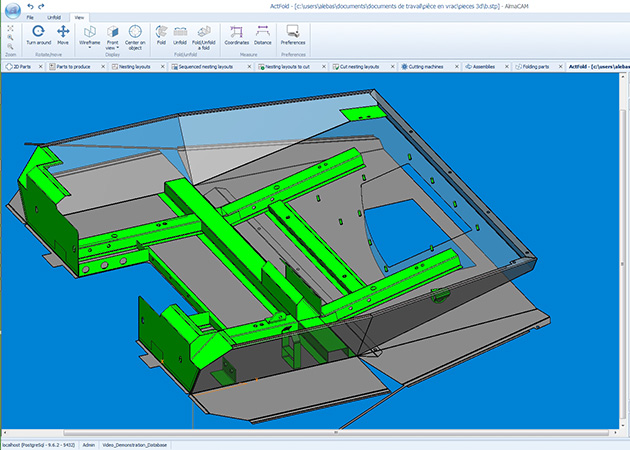
Automatiser l'imbrication des pièces et l'optimisation des trajectoires de coupe
Compte tenu de la quantité de pièces de tôle qui composent un navire, l’économie de matière que peut apporter le logiciel de FAO est le principal argument pour changer de logiciel d’imbrication. Car il y a des systèmes d’imbrication très performants, comme celui d’Almacam, et d’autres qui le sont moins. Il convient de noter qu’en termes navals, un gain de 1% dans l’utilisation des matériaux peut se traduire par une économie de plusieurs centaines de milliers de dollars sur la production annuelle d’un navire.
Un fournisseur de logiciels de FAO et de solutions d’imbrication devrait être en mesure de vous prouver son expertise et vous proposer de réaliser un benchmark basé sur des pièces réelles. C’est un moyen concret de vous faire prendre conscience de la valeur ajoutée d’une imbrication efficace.
Chez Alma, le développement d’algorithmes d’imbrication est la principale raison d’être depuis 1979. Les 30 000 utilisateurs d’Alma dans le monde entier sont la preuve que nos algorithmes d’imbrication sont certainement les meilleurs. Aujourd’hui, une équipe d’ingénieurs spécialisés travaille sur ce sujet, améliorant continuellement les algorithmes et en développant de nouveaux, afin de réduire encore le pourcentage de chute.
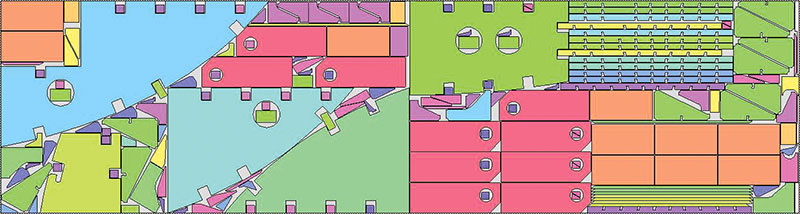
Maîtrise totale de la découpe au plasma, de la découpe des chanfreins et du marquage
Toute solution CFAO pour la construction navale doit tenir compte des spécificités liées à l’industrie et aux machines les plus courantes. Il est donc particulièrement important de maîtriser la découpe plasma (technique la plus utilisée en raison de l’épaisseur des tôles à découper).
Ainsi, parmi les fonctionnalités les plus utilisées, on trouvera la découpe en continu (pièces pontées pour minimiser le nombre d’avances et donc le temps d’usinage), la gestion des cerclages de tôles (laisser certaines ouvertures attachées à la pièce pour les besoins du transport), et la découpe du squelette (pour l’évacuer plus facilement).
Dans le domaine de la construction navale, il est également nécessaire d’avoir la capacité de gérer des machines produisant des chanfreins, et de gérer les opérations associées (multipasses, vérification de la hauteur, boucles de reconfiguration…) ainsi que des unités de marquage spécifiques. Ces opérations permettent notamment de tracer toutes sortes de textes qui sont utilisés pour l’assemblage ou le soudage des pièces.
Gérer des machines (très) spéciales
Mais ce qui contribue le plus à notre succès dans la construction navale, c’est notre capacité à gérer des machines spéciales. Pour ce faire, il faut s’appuyer sur une solution ouverte, permettant d’utiliser les fonctionnalités de base du logiciel de CFAO pour développer des applications totalement personnalisées.
Par exemple, avec Almacam, vous pouvez gérer des lignes de machines à « panneaux plats ». Ces machines assemblent et soudent des tôles pour ensuite découper une pièce particulièrement grande constituant un pont du navire, et enfin, souder les sections ou raidisseurs assurant sa rigidité et sa parfaite planéité. La machine utilisée pour la découpe peut également être utilisée pour effectuer d’autres opérations telles que le meulage, le marquage, le traçage de texte et le chanfreinage.
Un autre exemple de machines spéciales gérées par Almacam est celui des machines « symétriques ». Certaines machines symétriques peuvent marquer/découper simultanément des pièces bâbord et tribord qui sont « virtuellement » identiques. D’autres sont des machines à « double tête asynchrone » qui peuvent couper simultanément le haut et le bas d’une même pièce sans que les bords de coupe soient exactement parallèles.
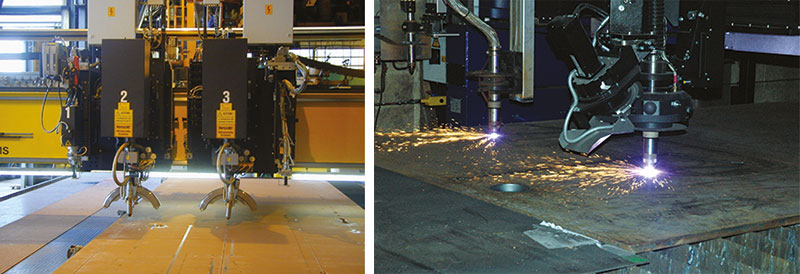
Automatiser le fonctionnement des logiciels
Une autre particularité de la construction navale est l’énorme quantité et la variété des pièces qui doivent être emboîtées et coupées. Cela nous permet d’affiner nos algorithmes d’imbrication automatique, et plus généralement nécessite que leur fonctionnement soit le plus automatisé possible : cela réduit les temps de programmation et les risques d’erreur.
Ainsi, la grande majorité des projets que nous déployons s’articulent autour des phases suivantes, réalisées et séquencées automatiquement :
- Importation des pièces avec préparation de l’usinage,
- Création des ordres de démarrage (regroupement par matière/pointe/bloc),
- Imbrication et génération des fichiers CN en mode batch.
Dans une dernière phase optionnelle, les ordres de démarrage sont clôturés afin de déclarer les pièces coupées et de mettre à disposition les chutes générées par les imbrications. Il est également important de noter que les documents mis automatiquement à la disposition des opérateurs et des programmeurs des machines sont presque toujours personnalisés, notamment pour répondre à la nécessité d’identifier les pièces découpées et de faciliter le tri.
Notre gamme de logiciels Almacam pour la découpe et le soudage 2D et 3D répond parfaitement à ces exigences propres à la construction navale.
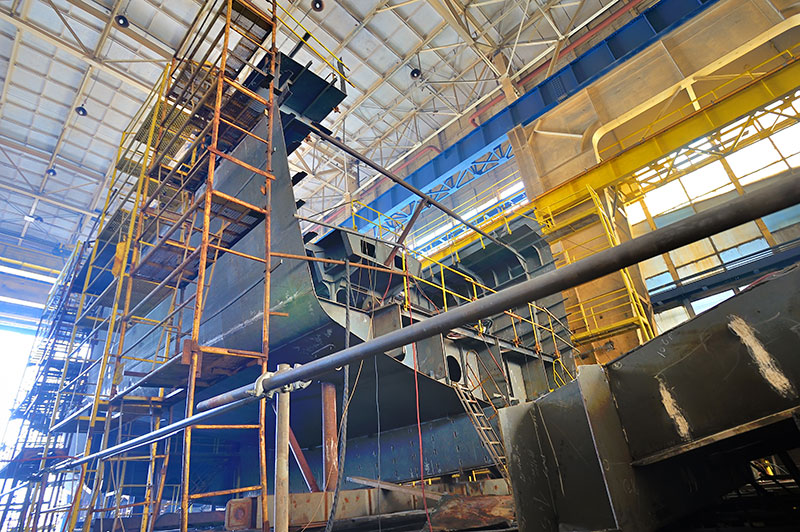
Gérer les processus de découpe linéaire et de soudage robotisé
Comme nous l’avons déjà mentionné, un navire est constitué de tôles et de sections assemblées par soudage, les sections ayant pour principale fonction de rigidifier la structure du navire. Les câbles et les tuyaux sont placés dans les sous-ensembles ou les blocs. Les aménagements intérieurs sont installés le plus tôt possible, mais après l’assemblage des premiers blocs.
Dans ce processus, Almacam est utilisé non seulement pour imbriquer et découper des pièces à partir de feuilles, mais aussi pour optimiser la découpe des sections. Nous avons ainsi développé différents algorithmes d’imbrication des sections pour maximiser l’utilisation des barres de matière première, tout en répondant aux exigences imposées par les machines que nous gérons (scies ou robots).
Par ailleurs, pour compléter notre savoir-faire, nous explorons les problématiques de soudage liées spécifiquement à la construction navale. Le logiciel Almacam Weld comporte de nombreuses fonctionnalités de reconnaissance géométrique automatique de formes 3D et de génération de tâches de soudage, ce qui nous permet de répondre aux besoins de programmation hors ligne des robots de soudage.
Quelle équipe pour vous accompagner ?
Pour mener à bien votre projet de chantier naval, les experts qui travaillent avec vous doivent avoir une approche partenariale forte et s’engager à vous fournir un service de haut niveau.
Au-delà des capacités techniques de nos logiciels de CFAO, la réputation d’Alma est le fruit de compétences acquises au fil des années grâce à des relations de confiance avec nos clients et des partenariats solides avec les différents acteurs du monde de la construction navale, en particulier les éditeurs de solutions de CAO et de PLM.
Cette expertise a été progressivement acquise en 40 ans et diffusée à l’ensemble des équipes commerciales et techniques de notre réseau. Elle nous permet d’aborder avec confiance et sérénité n’importe quel projet de construction navale dans le monde. Nous connaissons parfaitement les problématiques générales de la construction navale, mais aussi les spécificités liées aux différents types de navires ou à la localisation du chantier.
Nous travaillons avec les plus grands constructeurs européens de paquebots de croisière, et nous fournissons des équipements à de nombreux constructeurs de navires militaires et de transport de marchandises, partout dans le monde (Brésil, États-Unis, France, Italie, Allemagne, Chine, Inde, Indonésie, Corée, Japon, etc.)
Pourquoi Alma est-il le leader du marché de la CFAO pour la construction navale ?
La société Alma a commencé à explorer le monde de la construction navale en 1982. A l’époque, le chantier naval français de Saint-Nazaire cherchait un moyen de minimiser ses pertes de matériaux. Alma venait de mettre au point de puissants algorithmes d’imbrication automatique. Ce fut le point de départ d’une collaboration durable autour du logiciel Almacam. Depuis, l’outil de FAO n’a cessé d’être amélioré et l’équipe d’experts d’Alma a acquis une solide expertise. Aujourd’hui, Almacam est devenu une référence fiable pour les chantiers navals.
Minimiser les pertes de matériaux, le premier objectif à l’origine de la solution Almacam
Alma a commencé à explorer le monde de la construction navale en 1982. A l’époque, les Chantiers de l’Atlantique à Saint-Nazaire cherchent une solution pour minimiser leurs pertes de matière. Au regard des tonnes d’acier utilisées pour la construction d’un paquebot de croisière, cela représentait une économie plus que substantielle. Alma venait d’être créée, dans le but de promouvoir auprès de l’industrie les algorithmes d’imbrication automatique développés dans le cadre d’un projet de recherche de l’Université de Grenoble. Ce fut le point de départ d’une collaboration de longue date avec le chantier naval de Saint-Nazaire, mais aussi du développement et du déploiement de notre logiciel Cutting CAD/CAM pour la construction navale dans le monde entier. Aujourd’hui, ce logiciel nous permet de répondre à tous les besoins spécifiques de la construction navale et d’être reconnus comme l’acteur majeur de la CFAO pour la construction navale appliquée à la tôlerie.