Découpe robotisée de tubes et de profilés : un marché de niche occupé par des experts !
En partenariat avec des intégrateurs robotiques, en particulier Daihen Varstroj en Slovénie, Alma a adapté son logiciel de PHL à la découpe robotisée de tubes et de profilés. Un marché de niche qui répond à des problématiques précises chez les industriels et qui requiert une solutions machine + logiciel très élaborée. Ce type d’application illustre parfaitement la complémentarité entre l’intégrateur et l’éditeur de logiciels pour apporter une réponse sur-mesure au client, et la valeur ajoutée de la FAO dans le pilotage d’installations aussi complexes.
Pourquoi découper des tubes et des profilés à l’aide d’un robot ?
Les avancées technologiques de ces dernières années permettent désormais la réalisation de machines et de robots de découpe de tubes et profilés hautement automatisés et flexibles avec une mécanique de plus en plus sophistiquée. Classiquement, la découpe de tubes est réalisée par des machines laser avec une tête 5 axes. On peut notamment citer les machines de Mazak ou de Bystronic qui sont parfaitement optimisées pour la découpe laser, avec une multitude d’option dédiées. Mais ces machines peuvent être limitées à la découpe de tubes de petits diamètres et de relativement petite taille pour des raisons d’accessibilité. Pour découper des tubes de plus gros diamètre – en gros supérieur à 400 mm – et de plus grande taille, certains intégrateurs de robots conçoivent des cellules de découpe avec des bras robotisés en lieu et place des têtes 5 axes.
Les robots ayant un espace de travail de plus d’un mètre de rayon, ils peuvent découper des tubes et des profilés de toutes tailles sans contrainte d’accessibilité. De plus, grâce à l’utilisation d’un robot, ces installations sont beaucoup plus flexibles quant à la typologie de pièce à découper. Elles permettent non seulement de découper tous types de tubes (rond, rectangle, etc.) et de profilés (H, I, L, U, etc.) mais aussi de réaliser des pièces chanfreinées sur des tôles planes.
« Par exemple, un de nos clients découpe aussi bien des chanfreins sur des tôles de fortes épaisseurs que des tubes de 500 mm de diamètre ou des profilés H400 sur la même machine, » explique Nikola Smajgert, Project Manager chez Daihen Varstroj. « A coût égal, ces installations robotisées ont l’avantage d’une flexibilité et d’une productivité plus grande qu’en découpe 5 axes. »
Si la découpe robotisée de tubes et profilés constitue un marché de niche, elle intéresse de nombreux secteurs industriels (chaudronnerie, matériel de transport et agricole, BTP, etc.) et sa polyvalence permet d’ouvrir de nouveaux marchés aux clients qui y ont recours comme sous-traitants. Ces installations sur-mesure doivent cependant être parfaitement dimensionnées aux besoins des clients.
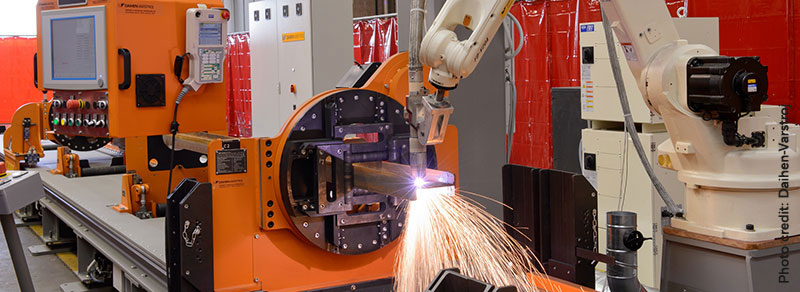
Comment fonctionnent les cellules robotisées de découpe de tubes et de profilés ?
Il existe deux types de cinématique pour les cellules robotisées de découpe de tubes :
- Les cellules avec un mandrin qui tourne et qui amène les barres devant le robot pour faciliter les configurations de découpe. Ces machines sont plus complexes mais permettent une meilleure qualité de coupe car la torche peut rester verticale.
- Les cellules sans mandrin, adaptées aux profilés qui ne nécessitent pas de découpe sous la barre. On peut alors se passer de la rotation du mandrin et simplement pousser la barre sur des rouleaux. Ce type d’installation moins onéreuse ne peut toutefois pas convenir à la découpe de tubes ronds et rectangulaires. En effet, l’accessibilité du robot est très difficile sur la position de début et de fin, et la matière fondue peut retomber sur la torche.
Sur ces installations, le plasma remplace la source laser car il a l’avantage d’être moins cher, efficace sur les gros diamètres et très facilement embarquable sur un bras robotisé. Le plasma permet aussi de découper des tubes et profilés de fortes épaisseurs et convient ainsi généralement mieux à la découpe de profilés.
Quid de la précision ?
Un des points d’attention est la plus faible précision d’un robot par rapport à celle d’une tête cartésienne. Elle reste cependant suffisante pour la découpe dans l’industrie lourde et les secteurs concernés.
Pour garantir une bonne précision, il est indispensable d’ajouter une stratégie de recalage de trajectoire pour compenser les inévitables déformations de la pièce. Plusieurs stratégies existent. Le palpage laser ou mécanique permet de connaitre la position réelle de points caractéristiques d’une barre et de recalculer les trajectoires en fonction des différences mesurées. Le contrôle de hauteur quant à lui permet d’adapter la hauteur de la torche pendant la découpe pour garantir une distance tôle/torche constante via une mesure de la tension.
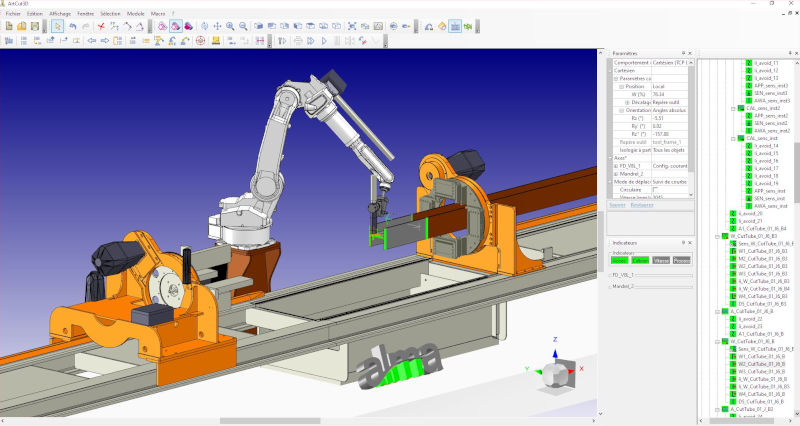
Pas de production sans un logiciel dédié
Bien qu’une grande majorité des robots soient pilotés par apprentissage, il est inenvisageable de piloter une cellule robotisée de plus de 6 axes à la console. A la fois pour garantir la précision de la pièce dessinée en CAO, mais aussi pour ne pas immobiliser la machine pendant la création de programme. « Sans un logiciel comme Almacam, ces machines seraient impossibles à programmer » confirme Nikola Smajgert.
Almacam Tube est capable de créer un programme robot à partir d’un assemblage CAO de manière totalement automatique. Via de puissants algorithmes de reconnaissance de tubes et profilés qui calculent les trajectoires à partir du modèle CAO, des algorithmes intelligents de nesting (imbrication) qui optimisent la position des pièces sur la barre et enfin des algorithmes optimisant les trajectoires robots pour éviter les collisions et singularités, la programmation de machines complexes est un jeu d’enfant !
Pour que cette automatisation fonctionne parfaitement, il est indispensable que le logiciel s’adapte à la machine et non l’inverse. Ainsi Almacam 3D permet une modélisation fidèle de la cinématique de la machine pour prévenir toute collision, prendre en compte les erreurs d’orientation inévitable et les corriger grâce à une calibration précise.
De plus, Almacam prend parfaitement en compte les stratégies de chargement, déchargement des tubes ou d’ouvertures de mors, ainsi que les paramètres de découpe automatiquement choisi en fonction de la matière et épaisseur de la pièce. Toute ces stratégies peuvent être personnalisée en fonction des contraintes propres à chaque machine.
Enfin, en étant capable de récupérer et traiter les données de production, le logiciel s’intègre complètement aux principes d’Industrie 4.0.
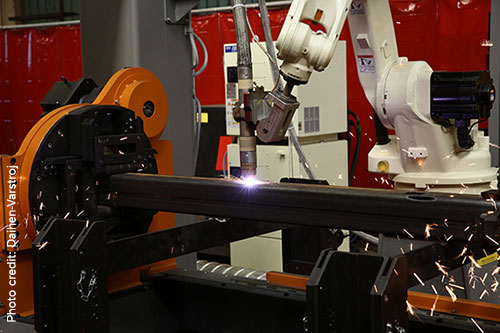
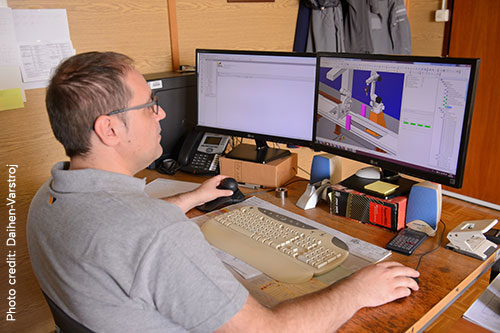
L’importance du partenariat entre l’intégrateur et l’éditeur
Pour la réussite d’un projet, l’expertise de l’intégrateur est plus importante que le choix de la marque du robot. Aussi il est indispensable d’avoir une bonne proximité entre le client, l’intégrateur robotique et l’éditeur de logiciels pour définir et optimiser les règles de fonctionnement de la machine. S’agissant d’installations qui peuvent nécessiter un an entre la configuration initiale et la livraison au client, il est essentiel de travailler ensemble dès le début du projet.
Par exemple, c’est grâce à de nombreux essais sur des pièces réelles que Daihen Varstroj et Alma ont mis au point des stratégies de palpage pour corriger les positions du robot en fonction des déformations des tubes ou des profilés, ces dernières étant inévitables sur des barres pouvant atteindre 12 mètres de long.
En conclusion, ce n’est pas un hasard si Almacam Tube est le logiciel leader en découpe de tubes robotisée, cette réussite tenant à trois facteurs :
- Une très forte expertise en découpe de tube à tous les niveaux du processus (import et modification d’assemblages de tubes, génération de trajectoires à partir d’un modèle CAO de tube, gestion des paramètres de découpe).
- Une expérience de 30 ans en programmation hors ligne de robots pour la découpe et la soudure (gestion de toute les marques de robots et calcul de trajectoires sans singularité ni collision).
- La très grande flexibilité du logiciel pour s’adapter aux besoins du constructeur et de l’utilisateur final.
Ce que résume Nikola Smajgert de son point de vue de partenaire : « Nous sommes très satisfaits du service et de l’expertise d’Alma, qui est à la fois un spécialiste du logiciel et de la robotique et qui connait parfaitement le métier du travail du métal. Notre coopération technique est très efficace, nous sommes sur la même longueur d’onde. C’est très important pour la réussite du projet chez le client. »
L’entreprise slovène Daihen Varstroj est un spécialiste de la soudure et de la découpe thermique. Filiale du constructeur de robots industriels japonais OTC-Daihen, Daihen Varstoj est le centre de production et de développement en Europe pour le groupe. Daihen Varstroj a une très grande expérience en installation de cellules robotisées, de systèmes de découpe de tôle au plasma, ainsi qu’en générateurs de soudure. Alma et Daihen Varstroj coopèrent depuis 2015 sur la commande de cellules robotisées et des tables de découpe 2D.