La découpe laser en continu de tôle en bobine avec DIMECO et Alma : un partenariat qui roule !
Publié le 31/05/2021
DIMECO est le spécialiste des systèmes de production à partir de tôles en bobines. Depuis sa création, l’entreprise familiale basée près de Besançon a su combiner son expertise technique de pointe avec un fort développement à l’international. Il y a huit ans, DIMECO lançait un système innovant de découpe laser en continu à partie de tôle en bobine. Adopté par des industriels de différents secteurs (équipement électrique, bâtiment, mobilier métallique, pièces automobiles, etc.) dans plusieurs pays, cette solution est pilotée grâce au logiciel d’Alma. L’imbrication optimisée sur des grandes longueur, la productivité du logiciel et son adaptation aux besoins spécifiques de chaque client sont à la base de ce partenariat fructueux.
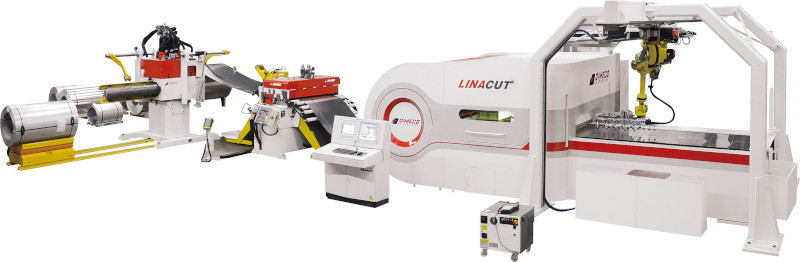
Une technologie novatrice
En 2013 au salon Tolexpo, DIMECO présentait en avant-première mondiale LINACUT®, sa ligne de découpe laser en continu des tôles en bobine. Grâce à ce procédé innovant, le constructeur a su combiner la flexibilité de la découpe laser avec la productivité du travail en bobines. Concrètement, l’installation est constituée d’une ligne de déroulage de bobines, d’un module de découpe laser en continu et d’un module de déchargement des pièces et d’évacuation des chutes. Ce système permet d’être alimenté par des bobines jusqu’à 25 tonnes pour des largeurs de tôle pouvant atteindre 2000 mm. Si les épaisseurs découpées sont le plus souvent comprises entre 2 et 2,5 mm, la machine est capable de travailler jusqu’à une épaisseur de 4 mm.
« La technologie de découpe laser en continu permet de produire en gros volume et de manière complétement automatisée de nombreuses pièces de formes et de tailles différentes, avec un niveau de déchets extrêmement bas » explique Thibault Nosbonne, ingénieur commercial chez DIMECO. Ainsi elle remplace avantageusement le poinçonnage-grignotage avec ses contraintes liées à la gestion des outils, même si DIMECO produit également des lignes de découpe en continu mixtes, qui combinent découpe laser et poinçonnage. Ceci permet par exemple de réaliser des pièces de formes complexes avec des emboutis. « L’autre intérêt de ce procédé en continu par rapport à la découpe laser en feuilles est de pouvoir découper des pièces de grande longueur, au-delà des capacités des machines laser standard », ajoute Thibault Nosbonne. En outre, pour les entreprises qui fabriquent leurs propres pièces (qui sont les principaux utilisateurs du système LINACUT®), le travail en bobine permet de rationnaliser la production et de réduire le poste d’achat de matière première, en mutualisant les épaisseurs de tôle ou les largeurs de bobines.
Dans la logique d’une production automatisée, le déchargement automatique des pièces et des déchets est un enjeu stratégique. Une bobine de 10 tonnes, 1500 mm de large et 1 mm d’épaisseur représente plus de 270 feuilles de 3 mètres de long. Bien entendu, le temps de changement d’une bobine est plus long que celui d’une nouvelle feuille, mais il faut le faire une seule fois : ceci, couplé aux systèmes automatisés de déchargement, procure une autonomie inégalée. Convoyeurs, robots, systèmes de préhension et de palettisation… DIMECO propose ainsi plusieurs procédés combinés à la machine pour évacuer, trier et empiler les pièces, chaque application étant adaptée aux besoins spécifiques du client.
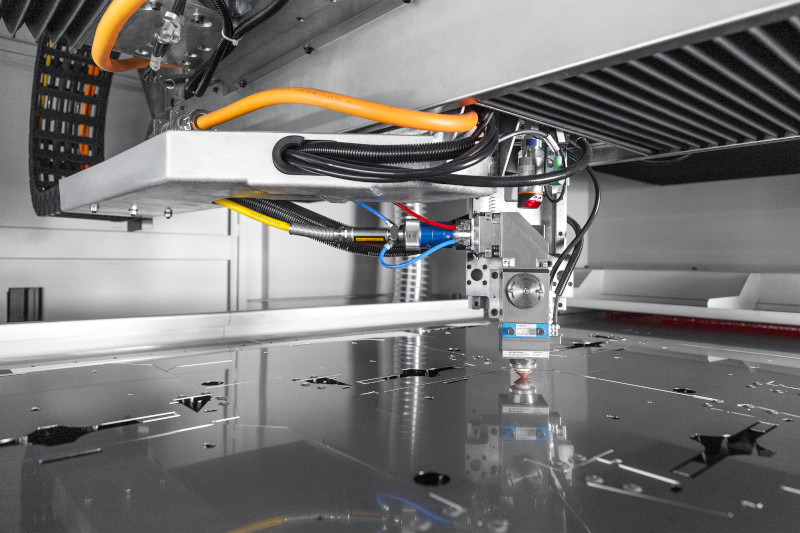
Le logiciel d’imbrication, une des clés de la solution LINACUT®
Pour être pleinement productif, découper en continu sur de grandes longueur implique d’utiliser un logiciel d’imbrication ad hoc. C’est la raison pour laquelle DIMECO a choisi dès le début de commercialiser ses machines LINACUT® avec le logiciel d’Alma, en France comme à l’international. Celui-ci a été jugé le plus efficace non seulement pour l’imbrication automatique des pièces de forme quelconques, mais aussi pour réduire les temps de programmation grâce à un fonctionnement intuitif et automatisé.
L’adaptation des algorithmes d’imbrication d’Alma aux particularités des machines LINACUT a fait l’objet d’un travail approfondi. « Le logiciel s’adapte parfaitement à la logique de fonctionnement de notre machine et permet d’atteindre d’excellents rendements matière, confirme Thibault Nosbonne. Une mise au point préalable avec l’utilisateur est cependant toujours nécessaire pour déterminer la meilleure stratégie de découpe compte tenu de sa production. »
Autre raison du choix de la solution Alma, la capacité de l’éditeur à développer des solutions spécifiques pour le client, en étroite relation avec le constructeur. Au-delà du post-processeur dédié à la machine, c’est particulièrement utile pour gérer les différents systèmes d’évacuation de pièces intégrés par DIMECO à la ligne de découpe en continu. Concrètement, le logiciel Alma transmet au système de préhension la position précise de chaque pièce et l’emplacement de dépose de la pièce, mais chaque client ayant ses spécificités, le pilotage de la palettisation fait toujours l’objet d’adaptations.
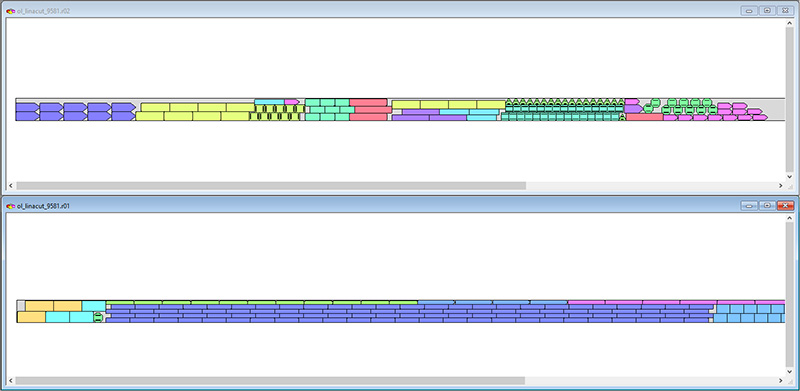
Une étroite collaboration entre le constructeur et l’éditeur
Dans ce contexte, la formation des utilisateurs finaux au logiciel est toujours assurée par Alma. Un ingénieur de DIMECO parfaitement formé au logiciel est par ailleurs pratiquement dédié au support des clients LINACUT® une fois le logiciel mis en place.
Tant dans la mise au point initiale de la solution que pour l’étude des besoins de chaque client, la collaboration entre l’éditeur de logiciel et le constructeur est primordiale. « Le niveau de maturité de notre partenariat avec Alma est très bon, constate Thibault Nosbonne. Nous travaillons très efficacement avec les ingénieurs d’application d’Alma qui ont bien compris les enjeux de la solution LINACUT®. »
De nouvelles évolutions du logiciel sont d’ailleurs en cours de test, notamment pour permettre de reprendre la découpe au milieu d’une imbrication, directement à la bonne zone, en cas de coupure de courant sur la machine par exemple. Une recherche continue de gains de productivité rendus possibles par un partenariat étroit et une vision commune à long-terme.